Big data in elevator maintenance
Repairing the elevator before it breaks down
Over twelve million elevators around the world move more than a billion people every day. That makes elevators the most frequently used mode of transport in the world – well ahead of cars, trains, buses, and planes. Measured in terms of daily trips, waiting times are already very low – but we want to improve them even further using a small, smart box called MAX that we developed in collaboration with Microsoft.
Elevator data in the cloud
Elevator data in the cloud
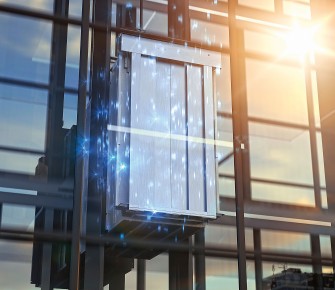
MAX continuously monitors and analyzes all the elevator’s data: How quickly is the door closing, how quickly is the elevator accelerating, what is the status of all its components? These data are sent to the cloud and analyzed there. If anything unusual is detected, the data are compared with all available data from thyssenkrupp’s entire elevator base. Have there already been cases where there were similar readings, indicating that a component is about to fail? This all takes place in a flash – and our service engineers receive a message on their smartphones in real time, such as: “A component needs replacing in the elevator on thyssenkrupp Allee.”
This enables us to repair the elevator before it breaks down, thus minimizing down times. For the people waiting in the lobby, it means as many elevators as possible are in operation. Or to put it another way, they won’t have to wait around because one of the elevators is out of order. MAX allows us to carry our proactive maintenance – all thanks to a small, smart box that is clairvoyant, math genius, and engineer all in one.